In today's dynamic and competitive landscape, organizations constantly seek ways to enhance efficiency, optimize processes, and deliver exceptional value. A powerful tool that facilitates this pursuit of excellence is the SQDCP board. This visual management system provides a structured framework for monitoring and improving key performance indicators across the organization. By fostering transparency, accountability, and collaboration, SQDCP boards empower teams to identify challenges, implement solutions, and drive continuous improvement.
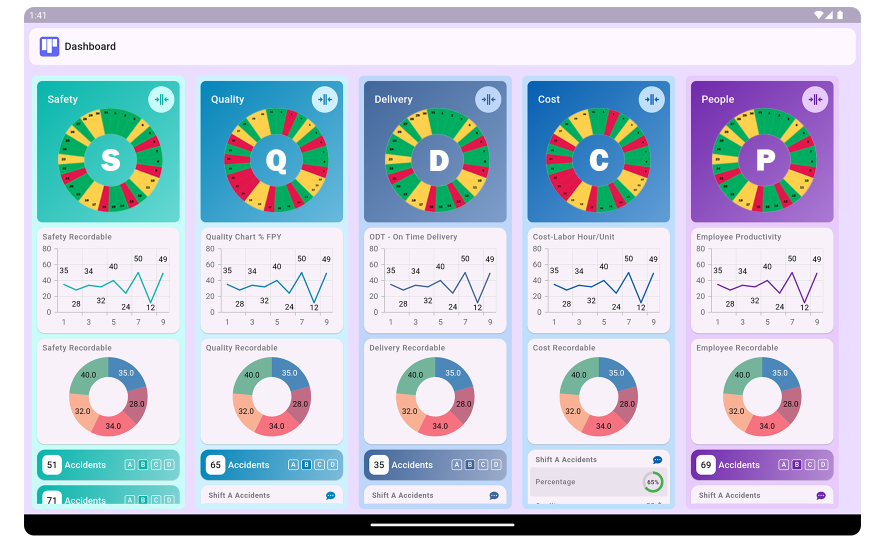
Understanding the SQDCP Framework
SQDCP is an acronym representing five critical areas of focus:
Safety
This pillar emphasizes the well-being of employees and the creation of a safe working environment. Metrics tracked might include the number of near misses, lost-time injuries, safety audit scores, and adherence to safety protocols. A strong safety record is paramount, not only for ethical reasons but also because it directly impacts productivity and morale.
Quality
Quality refers to the conformance of products or services to established standards and customer expectations. Key metrics could encompass defect rates, customer returns, on-time delivery performance, and customer satisfaction scores. Consistently delivering high-quality offerings is essential for building customer loyalty and maintaining a competitive edge.
Delivery
This aspect focuses on the timely and efficient delivery of products or services. Metrics might include lead times, on-time shipping rates, production cycle times, and order fulfillment accuracy. Meeting delivery commitments is crucial for customer satisfaction and operational efficiency.
Cost
Cost management involves tracking and controlling expenses associated with production, operations, and service delivery. Relevant metrics could include production costs per unit, material costs, overhead expenses, and energy consumption. Optimizing costs without compromising quality or delivery is a critical factor in profitability and sustainability.
People
This vital element recognizes the importance of employee engagement, development, and well-being. Metrics might encompass employee attendance rates, training completion rates, employee satisfaction surveys, and suggestions for improvement. A motivated and skilled workforce is essential for driving innovation and achieving organizational goals.
How SQDCP Boards Drive Continuous Improvement
SQDCP (Safety, Quality, Delivery, Cost, and People) boards are a structured visual management tool that helps organizations drive continuous improvement by providing real-time insights into key performance areas. These boards facilitate transparency, accountability, and data-driven decision-making across teams and departments.
1. Enhancing Visibility and Transparency
SQDCP boards make critical operational metrics visible to all team members, ensuring everyone is aligned with organizational goals. By tracking safety incidents, quality defects, delivery performance, cost efficiency, and workforce engagement, teams can quickly identify deviations and take corrective actions.
2. Promoting Data-Driven Decision-Making
By continuously monitoring performance metrics, SQDCP boards enable teams to make informed decisions. Patterns and trends become evident, allowing proactive problem-solving rather than reactive firefighting. This fosters a culture of continuous improvement by addressing inefficiencies before they escalate.
3. Encouraging Team Collaboration
Daily stand-up meetings around SQDCP boards promote collaboration among cross-functional teams. Regular discussions help in identifying bottlenecks, sharing best practices, and implementing corrective measures swiftly. This engagement drives team ownership and collective responsibility for process improvements.
4. Driving Root Cause Analysis and Problem-Solving
SQDCP boards facilitate structured problem-solving using methodologies such as the 5 Whys or fishbone analysis. When an issue is recorded, teams analyze its root cause, implement corrective actions, and track their effectiveness. This systematic approach ensures long-term solutions rather than temporary fixes.
5. Supporting Standardization and Continuous Monitoring
By consistently tracking SQDCP metrics, organizations establish standardized processes that enhance efficiency. Regular reviews ensure that improvements are sustained over time, leading to long-term operational excellence.
6. Boosting Employee Engagement and Accountability
By actively involving employees in monitoring and improving processes, SQDCP boards empower them to contribute ideas and take ownership of performance. This enhances engagement, motivation, and a culture of continuous improvement at all levels.
Benefits of Implementing SQDCP Boards
- Enhanced Transparency: SQDCP boards make performance data readily accessible to everyone in the organization, fostering a culture of transparency and accountability.
- Improved Communication: The boards serve as a focal point for communication, facilitating discussions about performance, challenges, and potential solutions.
- Data-Driven Decision Making: By visualizing performance data, SQDCP boards empower teams to make informed decisions based on facts rather than assumptions.
- Increased Collaboration: The regular meetings around the board encourage cross-functional collaboration and problem-solving.
- Continuous Improvement Culture: By regularly reviewing performance data and implementing corrective actions, SQDCP boards foster a culture of continuous improvement.
- Improved Performance: Ultimately, the goal of implementing SQDCP boards is to drive improvements in safety, quality, delivery, cost, and people, leading to enhanced organizational performance.
Implementing SQDCP Boards Effectively
- Define Clear Metrics: Identify the key performance indicators that are most relevant to the organization's goals and objectives.
- Set Realistic Targets: Establish achievable targets for each metric, based on historical data, industry benchmarks, and organizational capabilities.
- Ensure Data Accuracy: Implement robust data collection processes to ensure that the information displayed on the boards is accurate and reliable.
- Regularly Update the Boards: Keep the information current by updating the boards regularly, ideally daily or weekly.
- Conduct Regular Meetings: Schedule regular meetings around the board to review the data, discuss challenges, and identify opportunities for improvement.
- Empower Teams to Take Action: Give teams the authority and resources to implement corrective actions and drive improvements.
- Celebrate Successes: Recognize and celebrate achievements to reinforce positive behavior and motivate continued improvement efforts.
By implementing SQDCP boards effectively, organizations can create a powerful engine for continuous improvement, driving operational excellence and achieving sustainable success. The framework’s focus on key performance indicators, coupled with its emphasis on visual management and team collaboration, makes it a valuable tool for any organization striving to enhance its performance and achieve its strategic objectives.
FAQs: Driving Continuous Improvement with SQDCP Boards
1. What are SQDCP Boards?
SQDCP boards are visual management tools used to track and improve key performance metrics in five critical areas: Safety, Quality, Delivery, Cost, and People. They help teams identify problems, take corrective actions, and foster continuous improvement across the organization.
2. How do SQDCP Boards help in continuous improvement?
SQDCP boards provide real-time visibility into performance metrics, enabling teams to identify issues early, collaborate on solutions, and drive proactive improvements. Regular reviews ensure that processes are continuously monitored and improved over time.
3. What metrics are tracked on an SQDCP Board?
An SQDCP board tracks metrics related to Safety, Quality, Delivery, Cost, and People. These categories help organizations monitor and improve key performance areas that impact operational success.
4. How are problems identified and solved using SQDCP Boards?
When an issue is identified on an SQDCP board, teams conduct root cause analysis (e.g., using the 5 Whys method) to understand the underlying problem. Corrective actions are then implemented, and their effectiveness is tracked to ensure sustained improvement.
5. Can SQDCP Boards be used in any industry?
Yes, SQDCP boards are versatile and can be used across various industries, including manufacturing, healthcare, logistics, and service sectors. They help organizations improve their processes regardless of the industry they operate in.
6. How do SQDCP Boards promote team collaboration?
SQDCP boards encourage daily or weekly stand-up meetings where teams discuss performance metrics, share insights, and collaborate on solving problems. This fosters a culture of teamwork and accountability for improving processes.
7. How often should SQDCP Boards be updated?
SQDCP boards should be updated regularly, typically daily or weekly, depending on the business's operational pace. Frequent updates ensure that issues are addressed promptly and improvements are continuously monitored.
8. How do SQDCP Boards improve employee engagement?
By involving employees in the process of monitoring and improving key performance metrics, SQDCP boards promote ownership and accountability. This boosts morale and motivates employees to contribute to continuous improvement efforts.
9. What are the benefits of using SQDCP Boards over other improvement tools?
SQDCP boards offer real-time visibility, simplify problem-solving, and encourage team collaboration. Unlike other tools, SQDCP boards allow for immediate tracking of performance across multiple critical areas, helping to drive more comprehensive and sustainable improvements.
10. How do SQDCP Boards support a culture of accountability?
SQDCP boards visually track performance and issues, holding teams accountable for addressing problems. They create a transparent environment where everyone knows their role in driving improvement, leading to a stronger culture of accountability within the organization.