In the fast-paced world of manufacturing, maintaining clear visibility of performance metrics and improvement opportunities is crucial. The SQCDP Board, which stands for Safety, Quality, Cost, Delivery, and People, offers a comprehensive visual management system designed specifically for the shop floor. By presenting key metrics in a structured and straightforward way, SQCDP Boards empower teams to track, analyze, and respond to production issues efficiently.
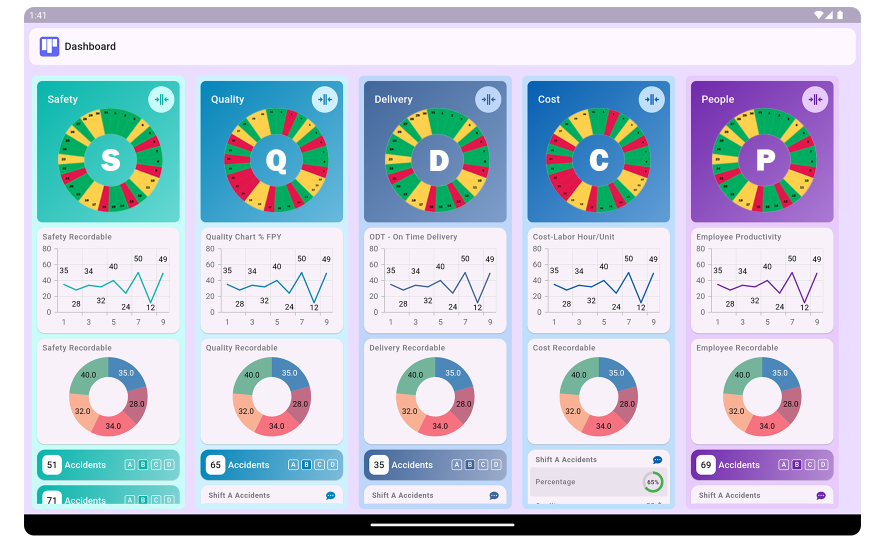
What is an SQCDP Board?
An SQCDP Board is a visual management tool that captures the five critical metrics necessary for efficient production:
- Safety: Prioritizes the health and safety of employees.
- Quality: Focuses on product standards and defect prevention.
- Cost: Tracks expenses and efficiency to manage costs.
- Delivery: Monitors on-time delivery and productivity.
- People: Emphasizes workforce engagement and well-being.
Together, these metrics provide a holistic view of a team’s performance on the shop floor. With clearly defined goals and visual indicators, SQCDP Boards make it easy for teams to identify and act on areas for improvement.
Key Components of an SQCDP Board
Each metric on the SQCDP Board has a dedicated section that provides actionable insights:
- Safety: Records incidents, near misses, and safety measures. Key performance indicators (KPIs) may include days without incidents and adherence to safety protocols.
- Quality: Captures defect rates, customer complaints, and compliance with quality standards. Common metrics are defect count and first-pass yield, reflecting the team’s ability to maintain high-quality production.
- Cost: Measures expenses related to materials, labor, and overhead. Tracking cost trends enables teams to minimize waste and improve operational efficiency.
- Delivery: Tracks adherence to production schedules and delivery timelines. Indicators like cycle time, lead time, and on-time delivery rates offer insight into productivity and timeliness.
- People: Focuses on engagement, attendance, and development. Employee satisfaction surveys, skill assessments, and training initiatives are commonly tracked to promote workforce well-being and skill enhancement.
These sections are typically color-coded (e.g., green, yellow, and red) to reflect performance levels and make it easier for teams to spot issues at a glance.
How Does the SQCDP Board Work?
The SQCDP Board functions as a daily communication tool. At the start or end of each shift, team members gather around the board to review current metrics, discuss issues, and set action plans. The visual and structured format allows teams to:
- Identify Gaps: Color-coded indicators provide an immediate view of problem areas.
- Analyze Root Causes: The team can investigate recurring issues and understand the underlying reasons for deviations in performance.
- Set Targets: Short-term, achievable targets keep the team focused on continuous improvement.
- Take Immediate Action: With data-driven insights, teams can address issues in real-time, preventing delays and inefficiencies.
This approach empowers shop floor teams to take ownership of their work and contribute to broader organizational goals.
Benefits of Using an SQCDP Board
Implementing an SQCDP Board provides several advantages:
- Enhanced Communication: Regular reviews of the SQCDP Board foster open communication between management and shop floor teams, ensuring everyone understands priorities and performance levels.
- Increased Accountability: By visually displaying metrics, the board encourages teams to take responsibility for their performance. Clear visibility promotes accountability, making it easier to follow up on improvement actions.
- Improved Efficiency: With a structured focus on Safety, Quality, Cost, Delivery, and People, teams are better equipped to make data-informed decisions, minimize waste, and enhance production efficiency.
- Proactive Problem-Solving: The daily or shift-based review system promotes proactive problem-solving, as teams can address minor issues before they escalate.
- Employee Engagement: Involving employees in daily performance discussions helps create a sense of ownership and pride in their work. The People section is particularly useful for tracking engagement and satisfaction levels.
Best Practices for Implementing an SQCDP Board
For successful implementation, follow these best practices:
- Set Clear Objectives: Ensure that each metric has well-defined goals, aligned with organizational priorities. Whether it’s reducing defect rates or improving safety compliance, clear objectives allow teams to measure success.
- Use Visual Indicators: Colors and symbols help team members quickly interpret data. Consider using green for meeting targets, yellow for moderate risk, and red for areas needing urgent attention.
- Hold Regular Reviews: Daily or shift-based reviews keep the board relevant and ensure timely responses to issues. During these reviews, encourage open dialogue and focus on constructive feedback.
- Encourage Team Participation: Allow team members to contribute to the board, whether by updating metrics or sharing insights. This involvement fosters a collaborative environment and boosts engagement.
- Document Action Plans: For each issue identified, create a clear action plan with responsibilities and deadlines. This structured approach ensures follow-through and accountability.
- Keep the Board Accessible: Place the board in a highly visible area, accessible to all team members. Accessibility reinforces transparency and ensures everyone is informed.
- Update Regularly: Keep data on the board current and accurate. Regular updates reflect the latest performance metrics and maintain the board’s relevance as a decision-making tool.
Tracking Progress and Measuring Success
The effectiveness of an SQCDP Board is directly related to the accuracy of the metrics and the commitment to daily reviews. Regular tracking allows teams to measure improvements over time, identify trends, and set progressive goals. Success can be evaluated through:
- Reduced Incidents and Defects: A decrease in safety incidents and quality defects signifies progress in these critical areas.
- Cost Reductions: Monitoring costs and identifying wasteful practices can lead to tangible savings.
- Improved Delivery Rates: Enhanced on-time delivery rates indicate better workflow and productivity.
- Increased Employee Engagement: Higher engagement and satisfaction levels often correlate with improved People metrics.
Conclusion
The SQCDP Board serves as an indispensable tool for visual management on the shop floor. By focusing on Safety, Quality, Cost, Delivery, and People, it provides a structured approach to monitoring performance and fostering continuous improvement. Through daily or shift-based reviews, shop floor teams can identify issues, take proactive steps, and ultimately enhance productivity. As businesses look to improve operational efficiency and engage employees, the SQCDP Board provides a reliable, visual solution for achieving consistent and measurable results.
The real value of the SQCDP Board lies in its ability to make complex data accessible and actionable. When implemented thoughtfully, this tool not only drives performance but also helps create a culture of accountability and teamwork, making it an asset to any production environment aiming for excellence.
1. What is an SQCDP Board?
The SQCDP Board is a visual management tool used on the shop floor to track and improve performance across five key metrics: Safety, Quality, Cost, Delivery, and People. It helps teams quickly identify and address issues to enhance operational efficiency.
2. How does the SQCDP Board work?
Teams review the board at the beginning or end of each shift, discussing current performance metrics, issues, and improvement actions. This regular review fosters proactive problem-solving and continuous improvement.
3. What does each letter in SQCDP represent?
- Safety: Health and safety on the shop floor.
- Quality: Product standards and defect prevention.
- Cost: Tracking of expenses to optimize costs.
- Delivery: Meeting production schedules and delivery timelines.
- People: Workforce engagement and well-being.
4. Why is the SQCDP Board important for manufacturing?
The SQCDP Board provides a real-time, visual overview of critical performance areas. It enables teams to respond swiftly to issues, promote accountability, and drive continuous improvements in safety, quality, efficiency, and engagement.
5. What are the benefits of using an SQCDP Board?
The SQCDP Board enhances communication, fosters accountability, improves efficiency, supports proactive problem-solving, and boosts employee engagement by making performance metrics visible and actionable.
6. How often should the SQCDP Board be reviewed?
Most teams review the SQCDP Board daily or at the beginning/end of each shift. Regular reviews ensure that issues are addressed promptly, allowing for real-time responses and continuous improvement.
7. How is progress measured on an SQCDP Board?
Progress is tracked through KPIs under each category (Safety, Quality, Cost, Delivery, People). Success is indicated by reduced incidents, lower defect rates, optimized costs, improved delivery timelines, and higher employee engagement.
8. Who is responsible for updating the SQCDP Board?
Typically, team leads or shift supervisors update the board with input from the team. However, involving team members in updates fosters engagement and accountability across the workforce.
9. Can an SQCDP Board be customized?
Yes, the SQCDP Board can be customized to reflect the unique goals and metrics of an organization. Customization helps tailor the board to specific operational needs and team objectives.
10. Where should the SQCDP Board be placed?
The SQCDP Board should be placed in a visible, accessible location on the shop floor where all team members can easily view and update it. Visibility encourages team participation and promotes transparency.