Overall Equipment Effectiveness (OEE) is a critical metric in the manufacturing industry that helps organizations measure and improve their production efficiency. OEE Monitoring and Reporting Software provides real-time insights into machine availability, performance, and quality, enabling manufacturers to optimize operations, reduce downtime, and enhance productivity.
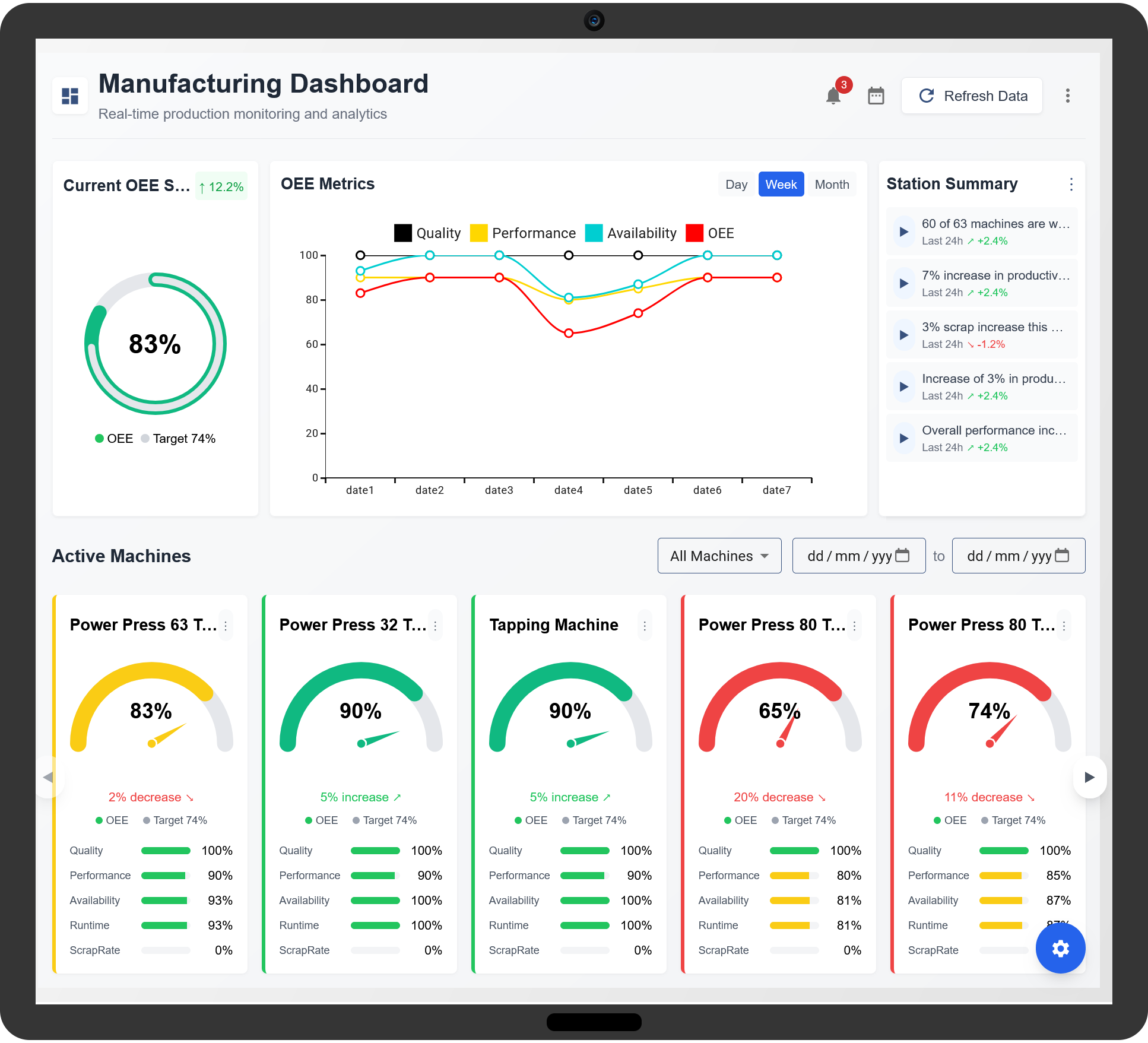
Understanding OEE in Manufacturing
OEE is a standardized method for measuring manufacturing productivity by assessing three key factors:
- Availability – Measures equipment uptime versus planned production time.
- Performance – Evaluates actual production speed against the ideal cycle time.
- Quality – Determines the percentage of defect-free products in total output.
A perfect OEE score of 100% means that a manufacturing unit is producing only good parts, as fast as possible, with zero downtime. However, most manufacturers operate at a much lower efficiency, making OEE monitoring software essential for identifying areas of improvement.
Key Features of OEE Monitoring and Reporting Software
1. Real-Time Data Collection
Captures machine data automatically from sensors, IoT devices, or production systems.
Monitors production trends, equipment performance, and downtime causes.
2. Automated OEE Calculation & Reporting
Calculates OEE scores instantly and provides visual dashboards.
Generates customizable reports for data-driven decision-making.
3. Downtime Tracking & Root Cause Analysis
Logs and categorizes downtime reasons to pinpoint recurring issues.
Helps maintenance teams proactively address equipment failures.
4. Performance Benchmarking & Historical Analysis
Compares production efficiency across shifts, lines, or plants.
Identifies patterns to optimize manufacturing workflows.
5. Integration with Manufacturing Systems
Connects seamlessly with ERP (Enterprise Resource Planning) and MES (Manufacturing Execution System).
Enables centralized data management and streamlined operations.
6. Custom Dashboards & Alerts
Provides interactive visualizations of OEE metrics.
Sends notifications for performance deviations or equipment failures.
Benefits of OEE Monitoring and Reporting Software
1. Increased Equipment Utilization
By identifying inefficiencies and tracking machine performance, manufacturers can maximize production uptime and reduce idle time.
2. Reduced Production Losses
OEE reporting software helps detect bottlenecks, slow cycles, and scrap rates, minimizing losses related to performance and quality.
3. Improved Decision-Making
Data-driven insights allow managers to make informed decisions, whether it’s scheduling maintenance, optimizing processes, or allocating resources.
4. Enhanced Product Quality
Monitoring defect rates and identifying quality trends ensures better product consistency and reduces rework or waste.
5. Lean Manufacturing Implementation
OEE tracking supports lean initiatives by eliminating waste, reducing downtime, and improving overall production efficiency.
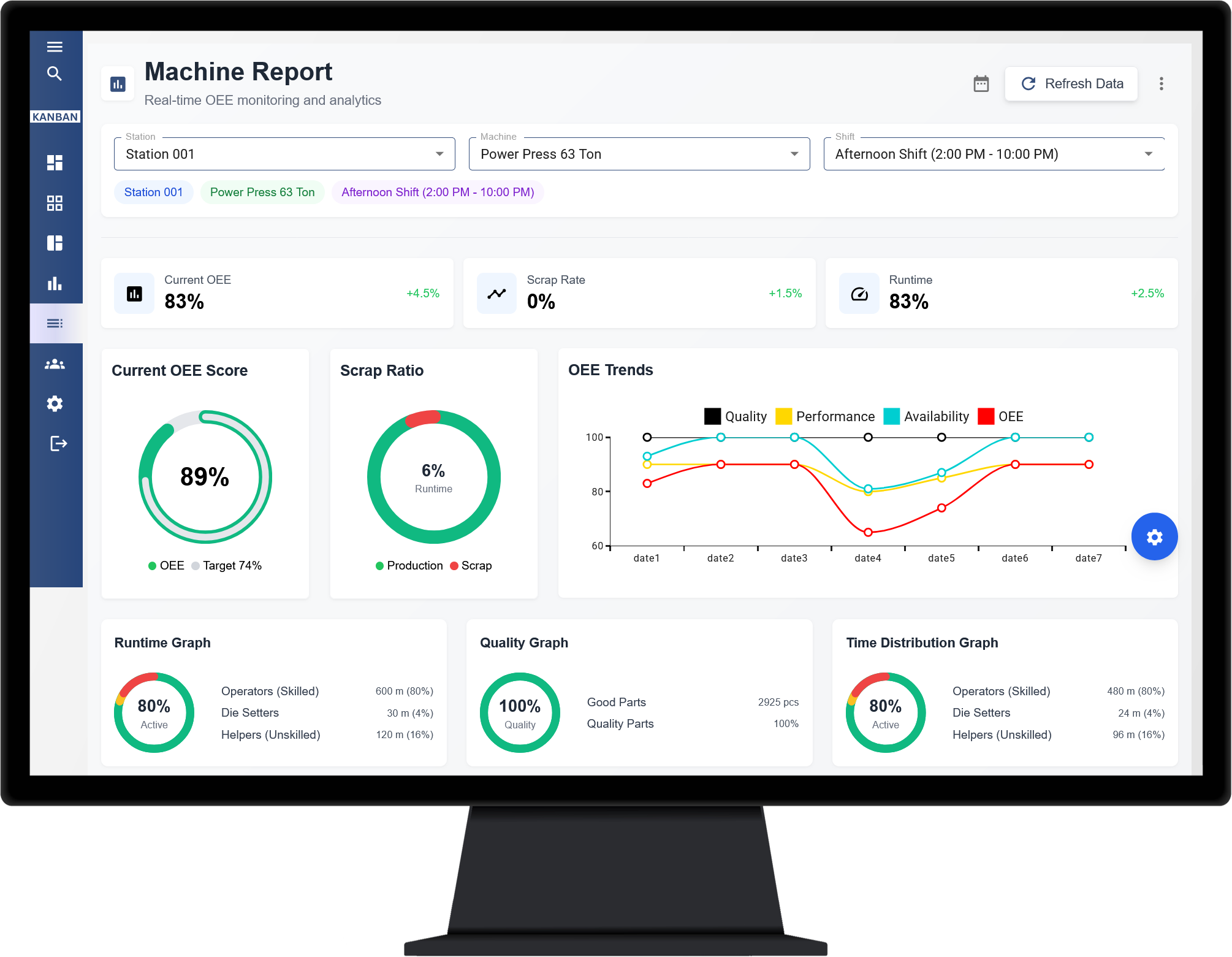
How OEE Software Transforms Manufacturing Operations
- Predictive Maintenance – By analyzing real-time machine data, manufacturers can schedule maintenance before failures occur, preventing unexpected breakdowns.
- Production Optimization – OEE insights highlight process inefficiencies, allowing for workflow adjustments that boost productivity.
- Workforce Productivity – Operators can track performance in real-time, fostering accountability and continuous improvement.
- Cost Reduction – Enhanced efficiency leads to lower energy consumption, reduced material waste, and optimized labor costs.
Implementing OEE Monitoring and Reporting Software in Manufacturing
Step 1: Define Goals & Metrics
Identify key performance indicators (KPIs) to track using OEE software.
Establish benchmarks for availability, performance, and quality.
Step 2: Integrate with Existing Systems
Connect the OEE software with shop floor equipment, ERP, and MES platforms for seamless data flow.
Step 3: Train Employees
Educate operators, maintenance teams, and managers on how to use OEE insights for process improvement.
Step 4: Analyze Data & Take Action
Regularly review OEE reports to identify trends, inefficiencies, and opportunities for enhancement.
Step 5: Continuously Improve
Use OEE data for continuous process improvement and implement corrective measures to achieve higher productivity levels.
Conclusion
OEE Monitoring and Reporting Software is a game-changer for the manufacturing industry, enabling businesses to track, analyze, and improve production efficiency. By leveraging real-time insights, automated reporting, and advanced analytics, manufacturers can reduce downtime, optimize resources, and drive continuous improvement. Investing in OEE software is a strategic move towards achieving lean manufacturing, enhancing competitiveness, and ensuring long-term success in the industry.
OEE Monitoring and Reporting Software for the Manufacturing Industry- FAQs
What is OEE Monitoring and Reporting Software?
OEE (Overall Equipment Effectiveness) Monitoring and Reporting Software is a digital solution designed to track, analyze, and report on manufacturing efficiency. It helps identify production losses, improve machine performance, and enhance productivity by providing real-time data on availability, performance, and quality metrics.
Why is OEE important for manufacturers?
OEE is crucial as it measures how effectively manufacturing processes utilize equipment. By identifying inefficiencies such as downtime, speed losses, and quality defects, manufacturers can optimize production, reduce waste, and improve overall efficiency.
How does OEE software improve productivity?
OEE software provides real-time insights into equipment performance, helping manufacturers detect bottlenecks, reduce downtime, and implement corrective actions. By continuously monitoring key performance indicators, businesses can achieve higher efficiency and reduced operational costs.
What key features should OEE software have?
Effective OEE software should include real-time data collection, customizable dashboards, automated reporting, root cause analysis, downtime tracking, and integration with other manufacturing systems such as MES (Manufacturing Execution System) and ERP (Enterprise Resource Planning).
Can OEE software integrate with existing manufacturing systems?
Yes, most OEE monitoring solutions are designed to integrate seamlessly with existing systems like MES, ERP, and SCADA (Supervisory Control and Data Acquisition) to ensure a comprehensive approach to performance tracking and optimization.
How does OEE software help reduce downtime?
By continuously monitoring machine performance, OEE software detects inefficiencies and alerts operators about potential issues before they cause significant downtime. It also provides detailed analytics to identify patterns and root causes of production disruptions.
Is OEE software suitable for all types of manufacturing industries?
Yes, OEE software is adaptable for various manufacturing sectors, including automotive, food and beverage, pharmaceuticals, electronics, and more. It helps any production-based business optimize equipment utilization and improve efficiency.
What are the benefits of automated OEE reporting?
Automated OEE reporting eliminates manual data entry, reduces errors, and provides real-time insights into production efficiency. It allows manufacturers to make data-driven decisions, streamline operations, and enhance continuous improvement efforts.
How does OEE software contribute to continuous improvement?
OEE software enables manufacturers to track performance trends, identify recurring issues, and implement process improvements based on real-time data. This systematic approach helps drive continuous improvement and lean manufacturing initiatives.
What factors should be considered when selecting OEE software?
When choosing OEE software, consider factors such as ease of use, integration capabilities, real-time data tracking, reporting features, scalability, and support services. A solution that aligns with your specific manufacturing needs will provide the most value.