Overall Equipment Effectiveness (OEE) is a key performance metric that measures the efficiency and productivity of manufacturing operations. By evaluating availability, performance, and quality, businesses can identify areas for improvement and optimize production. OEE data collection software automates data gathering, providing real-time insights that help organizations reduce waste and improve efficiency.
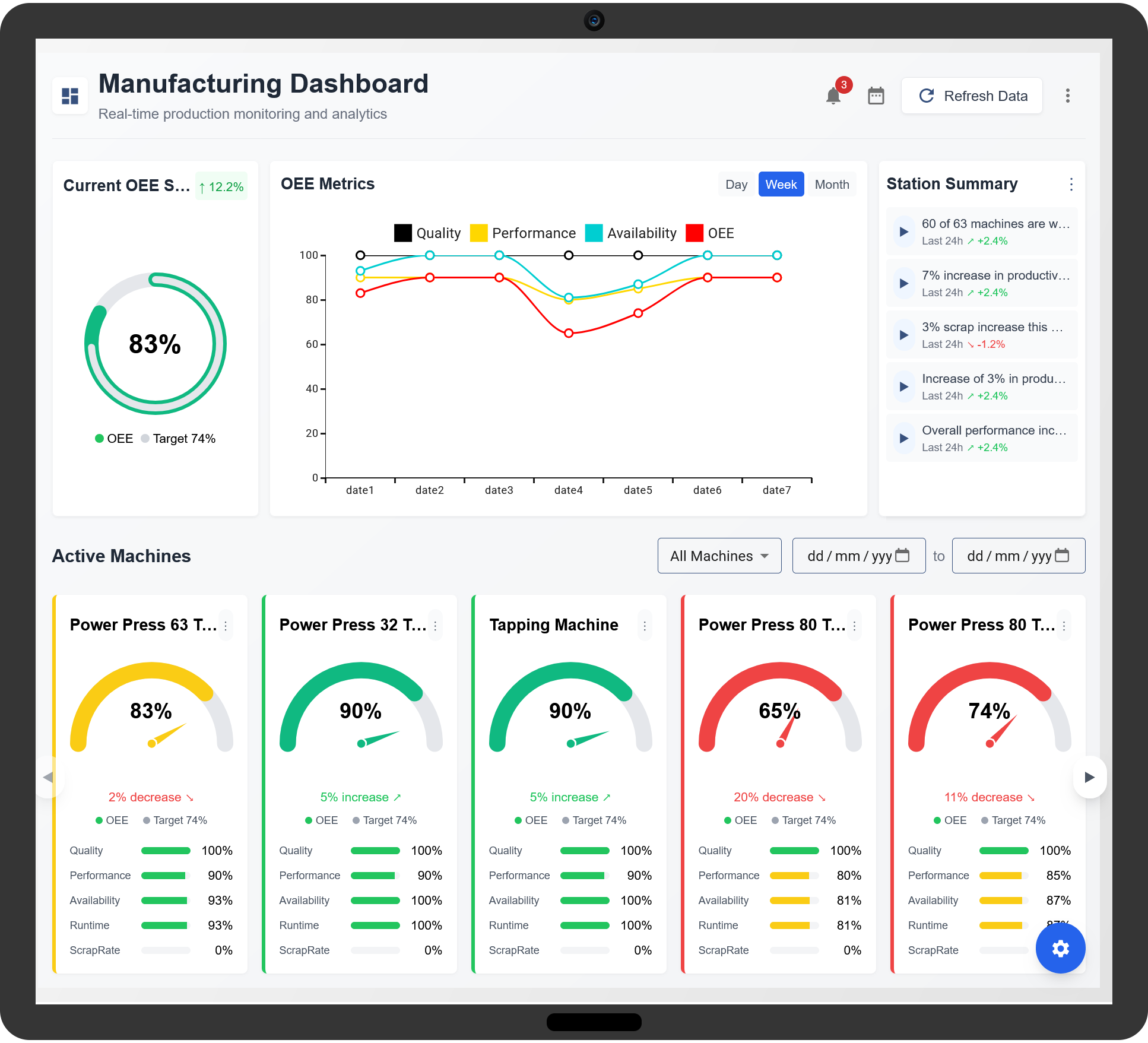
Understanding OEE and Its Components
OEE is calculated using three primary factors:
- Availability: Measures actual operating time against planned production time.
- Performance: Evaluates production speed compared to the maximum possible speed.
- Quality: Assesses the number of defect-free products produced.
A high OEE score indicates an optimized production process with minimal downtime, speed losses, and quality defects.
The Role of OEE Data Collection Software
OEE data collection software automates the process of gathering, analyzing, and visualizing machine performance metrics. Traditional methods rely on manual data entry, which can lead to inaccuracies and delays. By implementing an automated system, manufacturers can track real-time data, pinpoint inefficiencies, and make data-driven decisions.
Key Features of OEE Data Collection Software
- Real-time Monitoring: Provides live data on machine performance, reducing response time to issues.
- Automated Data Collection: Eliminates human errors and ensures data accuracy.
- Customizable Dashboards: Displays relevant performance metrics for different stakeholders.
- Integration with Existing Systems: Connects with production management systems for seamless data flow.
- Detailed Reporting and Analytics: Generates insightful reports to identify patterns and trends.
Reducing Waste with OEE Data Collection Software
Manufacturers face various types of waste, including unplanned downtime, inefficient processes, and defective products. OEE data collection software helps reduce these inefficiencies by:
- Minimizing Downtime: Identifies root causes of machine stoppages and suggests preventive actions.
- Improving Cycle Time: Tracks production speed deviations and optimizes machine settings.
- Enhancing Quality Control: Monitors defect rates and enables immediate corrective actions.
- Optimizing Resource Utilization: Ensures optimal use of materials, energy, and workforce.
Increasing Efficiency Through Data-Driven Decision-Making
By leveraging accurate and real-time data, organizations can enhance operational efficiency in several ways:
- Predictive Maintenance: Anticipates potential failures and schedules maintenance to prevent downtime.
- Standardized Workflows: Implements best practices for machine operations based on performance insights.
- Improved Workforce Productivity: Empowers employees with data-driven performance benchmarks.
- Continuous Improvement Initiatives: Supports lean manufacturing and Six Sigma methodologies.
Challenges in Implementing OEE Data Collection Software
While OEE data collection software offers significant advantages, some challenges include:
- Initial Implementation Costs: Investing in software and hardware upgrades.
- Integration with Legacy Systems: Ensuring compatibility with existing infrastructure.
- Employee Adoption: Training staff to effectively use the new system.
- Data Security Concerns: Protecting sensitive production data from cyber threats.
Best Practices for Successful Implementation
To maximize the benefits of OEE data collection software, businesses should:
- Start with a Pilot Project: Test the system on a small scale before full deployment.
- Ensure Stakeholder Buy-in: Educate employees and management on the software’s benefits.
- Integrate with Existing Systems: Seamlessly connect with MES and ERP solutions.
- Regularly Analyze Data: Continuously review insights to drive performance improvements.
Future Trends in OEE Data Collection
As technology advances, OEE data collection software is expected to evolve with:
- AI and Machine Learning: Predictive analytics for smarter decision-making.
- IoT Integration: Enhanced connectivity for real-time data transmission.
- Cloud-Based Solutions: Scalable and remote-accessible OEE monitoring.
- Automated Root Cause Analysis: AI-driven diagnostics for issue resolution.
Conclusion
OEE data collection software plays a crucial role in reducing waste and increasing efficiency in manufacturing environments. By automating data collection, providing real-time insights, and optimizing workflows, businesses can enhance productivity and achieve higher operational effectiveness. With the right implementation strategy, organizations can maximize the benefits of OEE monitoring, leading to improved profitability and sustainable growth.
FAQs: OEE Data Collection Software
1. What is OEE Data Collection Software?
OEE Data Collection Software is a digital tool that automates the monitoring and recording of production performance metrics, helping organizations optimize efficiency and reduce waste.
2. How does OEE software help in reducing waste?
By identifying inefficiencies such as downtime, speed losses, and quality defects, OEE software enables businesses to address production bottlenecks and reduce material waste.
3. Can OEE data collection software integrate with existing manufacturing systems?
Yes, most OEE software solutions can integrate with MES and ERP systems, providing seamless data flow and real-time insights across production processes.
4. What are the key features of OEE software?
Key features include real-time monitoring, automated data collection, customizable dashboards, integration capabilities, and advanced reporting tools.
5. How does OEE software improve production efficiency?
By continuously monitoring equipment performance and identifying downtime causes, OEE software helps in proactive maintenance and optimal resource utilization.
6. Is OEE data collection software suitable for all industries?
Yes, industries such as manufacturing, automotive, pharmaceuticals, food processing, and logistics benefit from OEE software to enhance productivity.
7. What are the common challenges in implementing OEE software?
Challenges include integration with legacy systems, employee adoption, data accuracy concerns, and initial implementation costs.
8. How secure is OEE data collection software?
Modern OEE software solutions include encryption, role-based access controls, and regular system audits to ensure data security and compliance.
9. Can OEE software support predictive maintenance?
Yes, by analyzing equipment data trends, OEE software helps predict potential failures and schedule maintenance before breakdowns occur.
10. What is the ROI of implementing OEE software?
Organizations see improvements in production efficiency, reduced downtime, lower operational costs, and increased profitability.
11. Key Features of OEE Data Collection Software
- Real-time Monitoring: Provides live data on machine performance, reducing response time to issues.
- Automated Data Collection: Eliminates human errors and ensures data accuracy.
- Customizable Dashboards: Displays relevant performance metrics for different stakeholders.
- Integration with Existing Systems: Connects with production management systems for seamless data flow.
- Detailed Reporting and Analytics: Generates insightful reports to identify patterns and trends.