In today’s fast-paced manufacturing and business environments, achieving operational efficiency and seamless workflow management is critical. One way to enhance efficiency is by integrating T-Card Software with Manufacturing Execution Systems (MES) and Enterprise Resource Planning (ERP) Systems. This integration ensures that real-time data flows between shop-floor operations and enterprise-wide planning, enabling businesses to optimize resource allocation, improve production tracking, and make data-driven decisions.
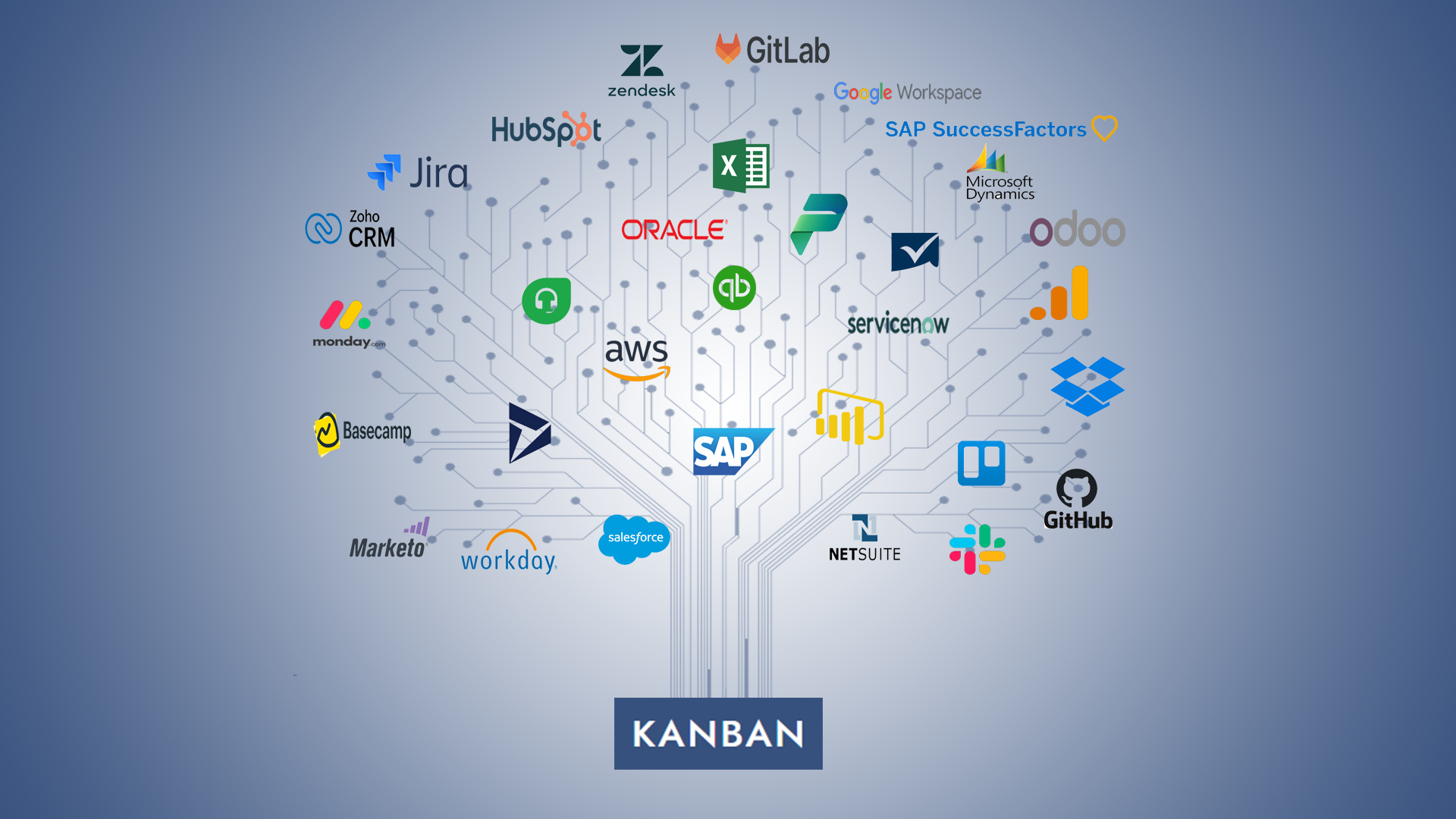
Understanding T-Card Software, MES, and ERP
T-Card Software
T-Card Software is a visual task management tool used to track and manage workflow processes. It provides a clear, structured approach to monitoring tasks, assigning responsibilities, and maintaining transparency in operations. Traditionally used in manual form, digital T-Card systems now allow automation, real-time updates, and enhanced data analytics.
Manufacturing Execution System (MES)
MES is a real-time production management system that tracks, monitors, and controls manufacturing processes on the shop floor. It connects machinery, operators, and production workflows to provide real-time data on work orders, material usage, and performance metrics.
Enterprise Resource Planning (ERP) System
ERP is a centralized system that integrates various business processes, such as finance, inventory, procurement, and human resources. It provides enterprise-wide visibility, facilitating data-driven decision-making and resource optimization.
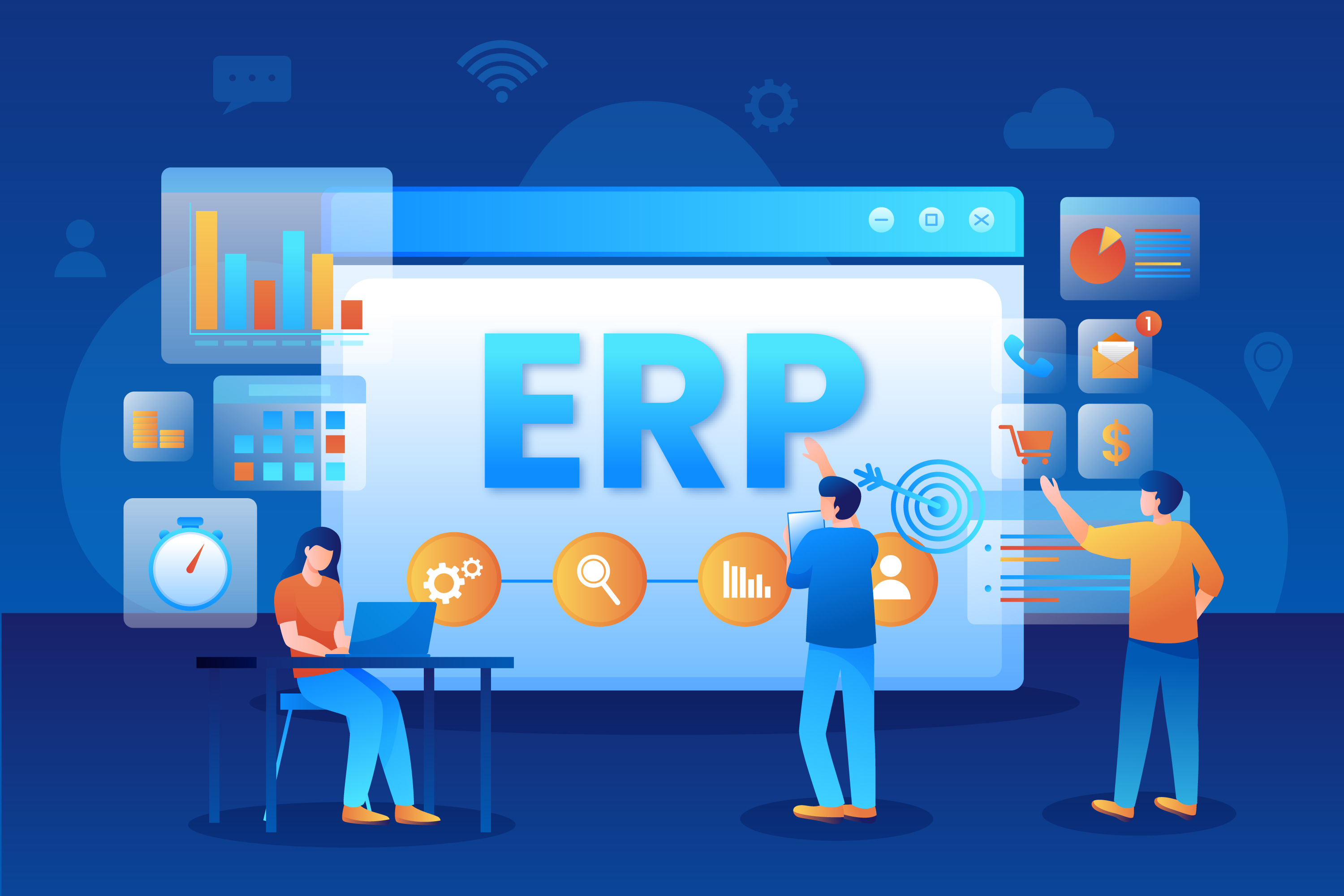
The Need for Integrating T-Card Software with MES and ERP
Businesses today require real-time data synchronization, automated workflows, and seamless collaboration between different departments. By integrating T-Card Software with MES and ERP systems, organizations can:
- Enhance production efficiency by aligning tasks and schedules with real-time shop-floor data.
- Eliminate manual data entry, reducing errors and improving productivity.
- Provide a unified view of operations, ensuring better decision-making.
- Improve workflow automation, enabling automatic task assignments and status tracking.
- Ensure seamless communication across production, planning, and administrative teams.
Key Benefits of Integration
1. Real-Time Data Synchronization
Integration enables instant updates between T-Card Software, MES, and ERP systems. This means that:
- Production teams receive real-time updates on work orders, job progress, and material availability.
- Management gains instant insights into operational performance, allowing quick adjustments to improve efficiency.
- Automated alerts notify teams of potential delays, enabling proactive problem-solving.
2. Improved Workflow Automation
T-Card Software enables automated task management, reducing the need for manual intervention. When integrated with MES and ERP, tasks such as:
- Job scheduling
- Work order management
- Inventory tracking
- Quality control checks
can be automated, ensuring smooth production processes and reducing downtime.
3. Enhanced Decision-Making
By consolidating data from T-Card Software, MES, and ERP, organizations gain a holistic view of operations. This allows them to:
- Identify inefficiencies and bottlenecks in production workflows.
- Optimize resource utilization by aligning workforce, materials, and machinery.
- Make data-driven strategic decisions to enhance overall business performance.
Challenges and Solutions
1. Integration Complexity
Merging different systems can be complex. Solution:
- Use a modular integration approach, implementing changes gradually.
- Work with experienced IT professionals to ensure smooth integration.
2. Data Accuracy and Consistency
Ensuring accurate data transfer between systems is crucial. Solution:
- Implement data validation protocols to reduce errors.
- Use real-time synchronization for consistency across platforms.
3. Resistance to Change
Employees may resist new technology. Solution:
- Conduct awareness programs to highlight benefits.
- Provide ongoing support and training to ease the transition.
Conclusion
Integrating T-Card Software with MES and ERP systems provides a powerful solution for organizations aiming to streamline operations, enhance workflow automation, and improve decision-making. By ensuring real-time data synchronization, automated task management, and seamless collaboration, businesses can achieve higher efficiency, reduce costs, and drive continuous improvement. Investing in integration today means better operational control and a competitive edge in the future.
1. What is T-Card Software, and how does it work?
T-Card Software is a digital task management system that helps organizations track workflows, assign responsibilities, and monitor progress visually. It replaces traditional manual T-Cards with automated tracking, real-time updates, and analytics.
2. Why should T-Card Software be integrated with MES and ERP systems?
Integrating T-Card Software with Manufacturing Execution Systems (MES) and Enterprise Resource Planning (ERP) systems enhances real-time data sharing, workflow automation, and operational efficiency. This ensures seamless coordination between shop-floor activities and enterprise-wide planning.
3. What are the key benefits of integration?
- Real-time data synchronization between production and management systems.
- Automated task management for smoother workflows.
- Improved decision-making through consolidated insights.
- Reduced manual errors and enhanced productivity.
- Seamless communication between departments.
4. How does integration improve workflow automation?
Integration allows automated job scheduling, work order management, inventory tracking, and quality control by ensuring that T-Card Software interacts dynamically with MES and ERP systems.
5. What industries benefit from this integration?
Industries such as manufacturing, logistics, healthcare, automotive, and aerospace benefit from improved workflow visibility, resource optimization, and efficient production management.
6. What challenges might arise during integration?
- Complex system compatibility between different platforms.
- Data accuracy and synchronization issues.
- Employee resistance to adopting new technologies.
- Implementation costs and time.
7. How can integration challenges be addressed?
- Use modular integration for phased implementation.
- Ensure data validation to maintain accuracy.
- Provide employee training to encourage adoption.
- Work with experienced IT professionals to ensure a smooth transition.
8. Can T-Card Software be customized for specific MES and ERP systems?
Yes, most T-Card Software solutions offer customizable APIs to ensure seamless integration with different MES and ERP platforms, adapting to specific business requirements.
9. What security measures should be considered during integration?
- Data encryption and secure access controls.
- Role-based permissions to protect sensitive information.
- Regular system audits to ensure compliance and security.
10. What is the ROI of integrating T-Card Software with MES and ERP?
Businesses typically see increased efficiency, reduced operational costs, faster production cycles, and improved decision-making, leading to higher profitability and sustainable growth.