In modern manufacturing, efficiency is a key factor in staying competitive. Overall Equipment Effectiveness (OEE) software plays a vital role in streamlining production processes, reducing downtime, and enhancing operational performance. By tracking availability, performance, and quality in real-time, OEE software empowers manufacturers to make data-driven decisions and optimize production workflows.
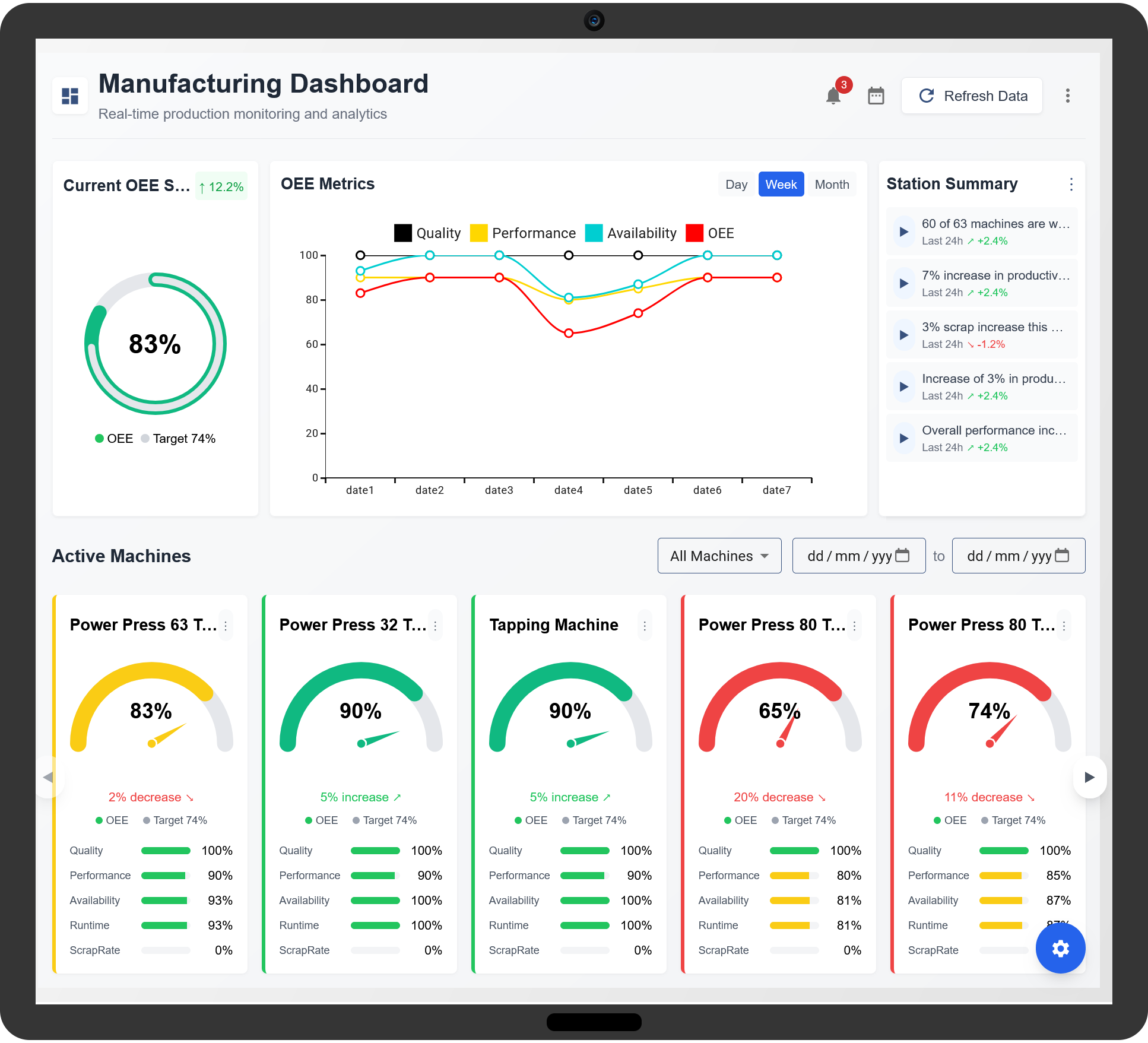
Understanding OEE in Manufacturing
OEE is a globally recognized metric used to measure production efficiency. It evaluates three critical factors:
- Availability – Measures equipment uptime versus planned production time.
- Performance – Assesses the actual production speed compared to the ideal cycle time.
- Quality – Determines the ratio of defect-free products to total output.
Key Features of OEE Software
- Real-Time Monitoring – Collects and analyzes production data in real-time.
- Automated OEE Calculation – Provides instant feedback on efficiency.
- Downtime Analysis – Identifies and categorizes root causes of downtime.
- Quality Management – Tracks defect rates and quality trends.
- Custom Dashboards – Displays interactive charts and reports.
- System Integration – Connects with ERP and MES platforms.
How OEE Software Helps Manufacturing Operations
Maximizing Machine Availability
OEE software detects the root causes of downtime, enables predictive maintenance, and optimizes machine utilization.
Improving Production Performance
It tracks production speeds, identifies inefficiencies, and reduces speed losses.
Enhancing Product Quality
By monitoring defect rates, identifying quality issues, and improving quality control, manufacturers can reduce waste and rework.
Data-Driven Decision-Making
Real-time reports provide insights into efficiency, enabling manufacturers to optimize workflows.
Reducing Manufacturing Costs
Optimized machine usage, lower energy consumption, and improved quality control contribute to cost savings.
Supporting Lean Manufacturing Practices
OEE software helps eliminate waste, improve efficiency, and drive continuous improvement.
Steps to Implement OEE Software Successfully
- Define OEE Objectives – Establish KPIs and set improvement goals.
- Integrate OEE Software – Ensure seamless data flow with existing systems.
- Train Employees – Educate teams on OEE best practices.
- Monitor and Analyze – Regularly review dashboards and reports.
- Optimize Continuously – Use insights to refine processes.
Challenges in OEE Implementation and Solutions
Resistance to Change
Solution: Involve employees early and emphasize benefits.
Data Accuracy Issues
Solution: Ensure reliable sensors and data collection methods.
Lack of System Integration
Solution: Choose software with ERP and MES compatibility.
Misinterpretation of Metrics
Solution: Train managers on data analysis and corrective actions.
Future of OEE Software in Manufacturing
- AI-Driven Predictive Analytics – Enhances maintenance and efficiency.
- IoT-Enabled Smart Manufacturing – Real-time monitoring with connected devices.
- Cloud-Based OEE Solutions – Enables remote monitoring and data access.
- Advanced Data Visualization – Improves decision-making with interactive reports.
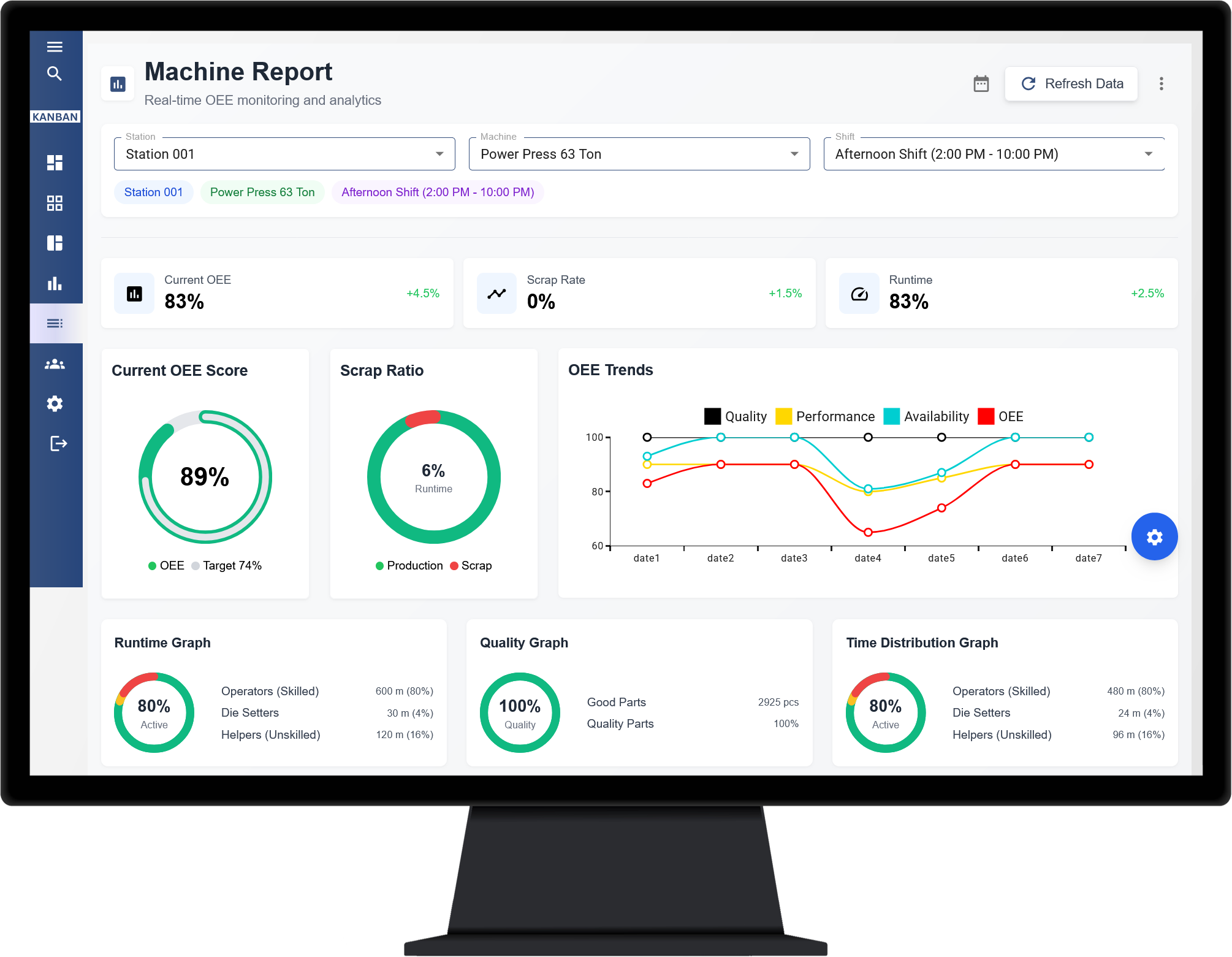
Conclusion
OEE software is a game-changer for manufacturing, offering real-time insights into machine performance, production efficiency, and quality control. With the right implementation, manufacturers can enhance productivity, reduce costs, and drive continuous improvement.
Top 10 FAQs on How OEE Software Helps Your Manufacturing Operations
1. What is OEE software?
OEE (Overall Equipment Effectiveness) software is a digital tool used to measure and improve manufacturing efficiency by analyzing machine availability, performance, and quality in real time.
2. How does OEE software improve manufacturing productivity?
OEE software identifies production bottlenecks, tracks machine downtime, and provides data-driven insights to optimize workflows, reduce waste, and enhance overall productivity.
3. Can OEE software reduce downtime in manufacturing?
Yes, OEE software helps detect downtime causes, provides predictive maintenance insights, and ensures quick corrective actions to minimize disruptions.
4. How does OEE software support quality control?
It tracks defect rates, identifies quality issues in real time, and helps manufacturers implement corrective measures to improve product quality and reduce rework.
5. Is OEE software compatible with existing manufacturing systems?
Most OEE software integrates with ERP, MES, and SCADA systems to ensure seamless data exchange and comprehensive operational insights.
6. How does real-time monitoring in OEE software benefit manufacturing?
Real-time monitoring allows manufacturers to track machine efficiency, identify issues instantly, and make quick data-driven decisions to enhance performance.
7. Can OEE software help reduce manufacturing costs?
Yes, by improving equipment utilization, minimizing downtime, and enhancing quality, OEE software helps manufacturers lower production costs and increase profitability.
8. How does OEE software help in Lean Manufacturing?
OEE software aligns with Lean principles by eliminating waste, improving production efficiency, and enabling continuous process improvement.
9. What industries benefit from OEE software?
OEE software is widely used in industries such as automotive, electronics, pharmaceuticals, food & beverage, and other manufacturing sectors to optimize operations.
10. How can manufacturers implement OEE software successfully?
Successful implementation involves setting clear goals, integrating the software with existing systems, training employees, monitoring key metrics, and continuously optimizing processes.