Lean manufacturing is a methodology that aims to minimize waste without sacrificing productivity. It focuses on streamlining operations, improving quality, and delivering value to customers. Digital T-Card Systems are a powerful tool within this framework, enhancing visibility, communication, and efficiency on the shop floor.
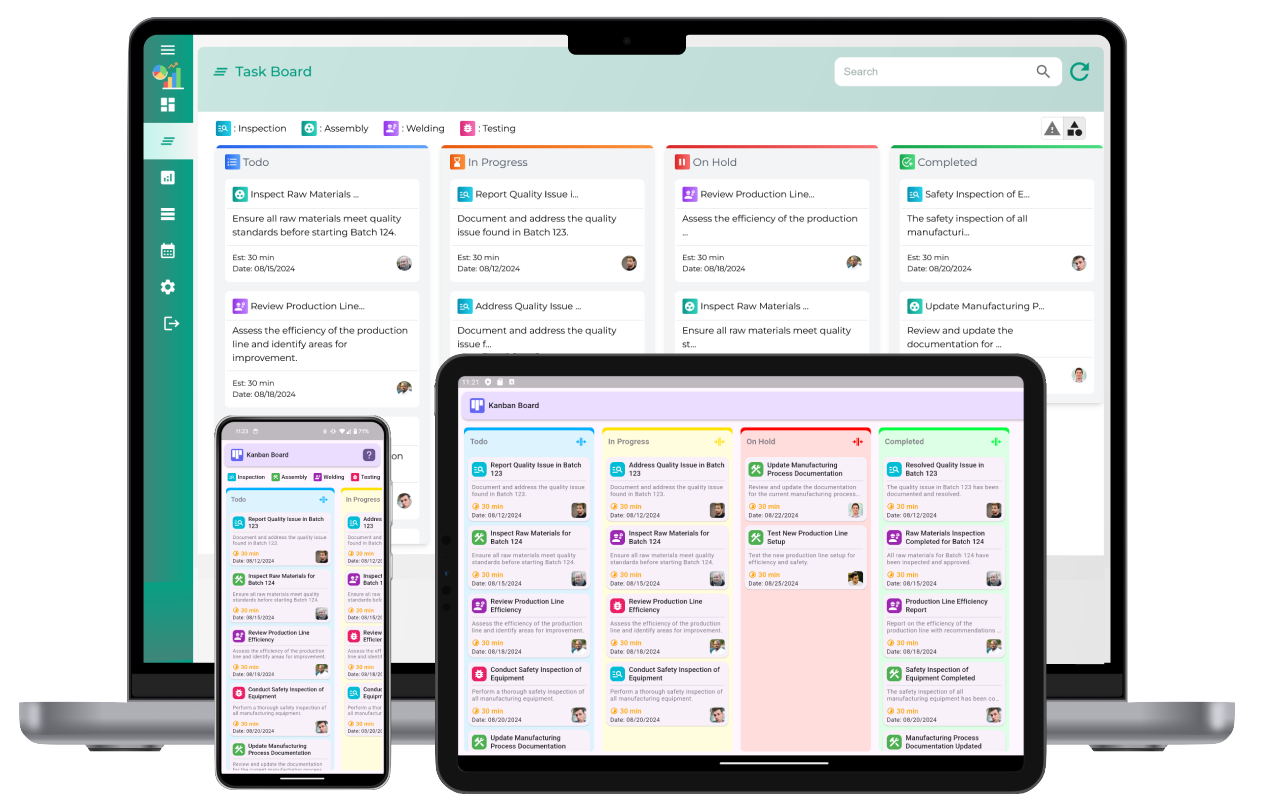
Understanding T-Card Systems
T-Card Systems originated as a simple visual management tool using physical cards on boards to track tasks, workflows, and inventory. Transitioning these systems to a digital format has provided numerous benefits, aligning perfectly with lean principles. Digital T-Cards facilitate real-time updates and remote access, allowing teams to manage tasks and workflows more effectively.
Key Benefits of Digital T-Card Systems in Lean Manufacturing
1. Enhanced Visibility and Communication
Digital T-Card Systems improve visibility across operations. Team members can see task statuses, inventory levels, and workflow bottlenecks at a glance. This transparency fosters better communication among teams, as everyone has access to the same real-time information. With the ability to update card statuses digitally, teams can promptly identify issues and address them before they escalate.
2. Streamlined Workflows
In lean manufacturing, optimizing workflows is crucial. Digital T-Cards allow organizations to visualize processes, helping to identify non-value-added activities and areas of improvement. By analyzing task flows, companies can streamline operations, eliminate unnecessary steps, and reduce cycle times, leading to more efficient production processes.
3. Improved Resource Management
Effective resource management is a core principle of lean manufacturing. Digital T-Card Systems help organizations monitor and allocate resources efficiently. With real-time data on task assignments and progress, managers can optimize workforce distribution and minimize idle time. This ensures that resources are used effectively, enhancing overall productivity.
4. Data-Driven Decision Making
One of the most significant advantages of digital systems is the ability to collect and analyze data. Digital T-Card Systems generate valuable insights that inform decision-making processes. By tracking performance metrics and analyzing trends, organizations can make informed decisions that align with lean principles, fostering a culture of continuous improvement.
5. Flexibility and Scalability
Lean manufacturing environments often require flexibility to adapt to changing market demands. Digital T-Card Systems are inherently scalable, allowing organizations to adjust their processes as needed. Whether adding new projects or reallocating resources, digital systems provide the agility necessary to respond to dynamic production environments.
6. Facilitating Continuous Improvement
Continuous improvement is at the heart of lean manufacturing. Digital T-Card Systems support this by enabling regular reviews of processes and performance. Teams can easily track progress, celebrate achievements, and identify areas for further improvement. This iterative approach helps cultivate a culture of excellence within the organization.
7. Integration with Other Systems
Digital T-Card Systems can integrate with various tools and technologies within an organization, such as Enterprise Resource Planning (ERP) systems or project management software. This integration ensures that all data is aligned and accessible in one central location, enhancing collaboration and information sharing.
8. Enhanced Accountability and Ownership
By assigning tasks to specific team members and tracking their progress, digital T-Card Systems promote accountability. Employees can see their contributions to overall productivity and are more likely to take ownership of their responsibilities. This accountability drives performance and fosters a sense of pride in one's work.
Implementing Digital T-Card Systems
1. Define Objectives
Before adopting a digital T-Card System, organizations must identify their goals. Whether the focus is on improving visibility, reducing waste, or enhancing communication, having clear objectives will guide the implementation process.
2. Select the Right Software
Choosing the appropriate software is crucial. Organizations should look for systems that align with their specific needs, offering features like real-time updates, data analytics, and integration capabilities.
3. Train Employees
Successful implementation hinges on employee engagement. Providing comprehensive training ensures that team members are familiar with the digital system and understand its benefits.
4. Monitor and Adjust
Post-implementation, organizations should regularly monitor the system's performance and gather feedback from users. Continuous evaluation allows for adjustments to improve efficiency and effectiveness.
Conclusion
Digital T-Card Systems are a vital component of lean manufacturing, driving efficiency, transparency, and continuous improvement. By embracing these systems, organizations can enhance their operational processes, improve resource management, and foster a culture of accountability and ownership. As manufacturing landscapes continue to evolve, digital tools like T-Card Systems will play an increasingly important role in helping organizations adapt and thrive in a competitive market.
1. What is a Digital T-Card System?
A Digital T-Card System is a software-based tool used for visual management and workflow tracking in manufacturing. It allows teams to manage tasks and resources effectively in real-time.
2. How does a Digital T-Card System enhance lean manufacturing?
It enhances lean manufacturing by providing real-time visibility into workflows, allowing for the identification and elimination of waste while improving resource management and efficiency.
3. What are the key features of Digital T-Card Systems?
Key features typically include task tracking, real-time updates, visual dashboards, integration with other software systems, and reporting capabilities.
4. Can Digital T-Card Systems be customized for different manufacturing processes?
Yes, these systems can be tailored to fit various manufacturing processes, allowing organizations to adapt them to their specific operational needs and workflows.
5. How do Digital T-Card Systems facilitate communication among team members?
By providing a shared digital platform for tracking tasks and progress, these systems ensure that all team members are on the same page, which enhances collaboration and communication.
6. What role does data analytics play in Digital T-Card Systems?
Data analytics help organizations analyze performance metrics, track efficiency, and identify trends over time, which supports continuous improvement efforts.
7. Are Digital T-Card Systems easy to implement?
While the ease of implementation can vary, most Digital T-Card Systems are designed to be user-friendly. Proper training and support during the implementation phase can greatly facilitate the process.
8. How can organizations ensure successful adoption of a Digital T-Card System?
Successful adoption involves clear communication of benefits, comprehensive training for users, and ongoing support to address any challenges that arise during use.
9. What are the costs associated with Digital T-Card Systems?
Costs can vary widely based on the features and functionalities required. Organizations should consider both initial setup costs and ongoing subscription or maintenance fees.
10. Can Digital T-Card Systems integrate with existing manufacturing software?
Yes, many Digital T-Card Systems are designed to integrate with existing software solutions, such as ERP systems, enhancing overall operational efficiency.